Digital mobile maintenance: Reduce production line downtime and increase productivity using predictive maintenance
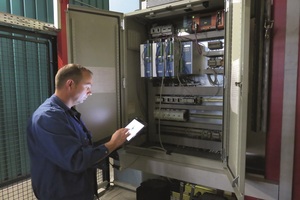
Mobile tablet solution offers direct accessto all machine data on every piece of machinery
Digital mobile maintenance is a technique for quickly and easily making production process productivity improvements for minimal investment through the application of digitalisation as part of an Industry 4.0 plant implementation programme.
Manufacturing maintenance specialists are already using tablet computers to directly access key machinery digital equipment histories, documents and PLC programs on site. However, they can also gain extra operational benefits by importing machine data directly from the PLC to the tablet. Such an approach can allow, for example, for the integration of additional predictive maintenance process instruction re-programming, extending the life of existing machines and preventing line breakdowns caused by catastrophic tooling failures.
Now this process improvement can be achieved by integrating HARTING’s MICA, a Modular Industrial Computing Architecture edge computer, which can communicate data between the different machine proprietary operating systems and directly forward it to an operator’s tablet device. MICA can also store and process the data in accordance with pre-determined operational maintenance limits, and consequently operators can arrange modification to PLC programming as appropriate, thus optimising processes and reducing machine downtime.
MICA is reportedly compact, has a degree of protection rating of IP67 and can easily be located directly on the machine, which may be operating in harsh environmental conditions. Alternatively, a DIN rail mounting option is available for location within the machine’s control cabinet.

Modular hardware permits customer-specific adaptation, while modular software ensures increased reliability and ease of development
There are no operating restrictions with MICA. Open software architecture runs in virtual Linux based containers on top of a streamlined base operating system. Each application runs “sandboxed” in its own container with all libraries and drivers. Communication between containers requires a separate IP address, ensuring data security.
Standard containers are available from HARTING’s web site for downloading systems such as Java, Python, C/C++, OPC-UA, databases and Web toolkits. Standard tools (e.g. HTML5 and JavaScript) are used to programme and maintain MICA, making it very user-friendly for people with basic IT knowhow skills. The system is customisable so that other containers can be accommodated. This also means that it is potentially able to communicate with most existing machine operating systems.
In addition to solutions to technical challenges such as digital mobile maintenance, digitalisation projects highlight new ways of co-operation between inter-company departments. This highlights one of the great benefits about digitalisation: it enables organisations to better connect their systems with one another and also with their employees.
MICA enables integration of higher levels of intelligence into existing manufacturing plants for Smart Factory deployment. It provides the pre-analytical link between the factory-floor sensor level and the analytical/big-data cloud. Most importantly, it supports production process improvements including lower complexity and increased modularity, and facilitates cost reduction.
Comment on this article below or via Twitter @IoTGN