How IIoT is helping manufacturing businesses with global growth
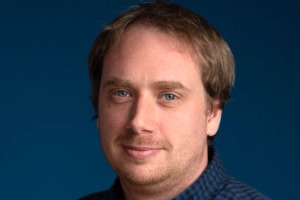
Ben Sturgess of Pathfindr
Despite growing challenges including spiralling costs and increased global competition, manufacturers continue to play a major role in the global economy, contributing US$6.7 trillion (€5.8 trillion) according to recent figures by Make UK, says Ben Sturgess, co-founder and chief technology officer, Pathfindr.
Currently the world’s eighth largest industrial nation – where manufacturing makes up 44% of total UK exports and employs 2.6 million people. With ongoing innovation in manufacturing sparking consumer demand and vice versa, there are substantial opportunities for businesses looking to grow, and for most this will mean looking at how they can expand their global reach. But with growth comes risk, and many companies will need to mitigate issues they have not encountered before. This includes tracking their assets on a much larger scale.
With this in mind, manufacturers will need to remain agile and have a well-thought through growth strategy if they’re going to succeed. These plans should include how they are going to utilise established and emerging digital technologies to facilitate growth plans. Real-time visibility and insight into their assets and processes will be critical for those looking to grow their operations, and data from industrial internet of things (IIoT)-connected devices is allowing manufacturers to identify where efficiency gains can be made and providing operational visibility. As part of the wider IIoT sector, asset and process intelligence is also enabling businesses to maintain operational control and efficiency while they expand. Below we explore some of the benefits.
Reducing asset wait time
In competitive environment, waiting and delays during manufacturing have a major impact. Just-In-Time (JIT) production models require that goods are delivered within the exact production window and there is significant pressure on manufacturers to meet this deadline. This places a premium on early visibility on issues in meeting targets and commitments, especially for businesses looking to operate in countries all around the world.
As manufacturers look to eliminate inefficiencies and become leaner, they could also benefit from trying to produce a ‘total-cost-of-waiting’ metric. Important questions to explore include: Do I know where my assets are? How long have they been there? When was the last time they were used? What condition are they in?
Once a business has an exact figure for what waiting is costing them and how much money could be saved by working more efficiently, then they will be in the right frame of mind to implement change.
Asset intelligence platforms and the adoption of advanced analytics provide an effective and immediate way to identify and eliminate the hidden factory. By reducing process inefficiencies, manufacturers will also be able to maximise employee productivity, allowing them to focus more heavily on tasks that drive more value for the business.
Remote monitoring
For businesses wanting to expand, one of biggest challenges to overcome is tracking their assets on a global scale. Unless manufacturers have real-time visibility of where assets are in the supply chain, it will be almost impossible to keep tabs on every single item going out into the field.
The use of asset intelligence – in this case using GPS-enabled devices – is gaining traction because it extends operational visibility to all parts of a manufacturing organisation, and then outwards – back to suppliers and forward to end-user customers. By definition it supports the fundamental approach of cellular manufacturing, where wastage is eliminated as far as possible, and adds value to other fast-moving industries where the rapid, flexible redeployment of assets is demanded. In these situations, dynamic location and related intelligence can reduce risk, increase speed and save money.
Losing items not only has severe implications for time and resource, as employees work to try and locate missing items as well as dispatch replacements, but also risks irreparable damage to customer relationships. Using GPS trackers, for example, will provide manufacturers with accurate, minute-by-minute data on where their assets are located, which is especially important when operating on a global scale with potentially multiple distribution and delivery partners.
Environmental monitoring and predictive maintenance
Remote monitoring does not only apply to location, as these trackers can also provide vital insight when it comes to environmental condition. For example, if temperature-sensitive pharmaceutical products are being transported across the globe, their condition can be remotely monitored to ensure they remain viable. While the trackers collect data on a range of environmental variables including temperature, humidity, air quality and pressure, it can also alert manufacturers to an issue before it has even had chance to arise, ultimately helping to increase an asset’s lifespan.
With The Annual Manufacturing Report finding that almost four in five businesses believe they have the capacity for growth, investment in digital technologies can help to increase productivity and efficiency, while also ensuring that they have the infrastructure in place to benefit from further innovation in future. Asset and process intelligence is one part of IIoT which is already having a huge impact, and as the technology becomes more powerful and simultaneously cheaper, we expect to see a significant increase in uptake driven by businesses expanding their operations globally.
Pathfindr’s award-winning industrial IoT solutions provide customers with real-time insights into their assets and processes, from indoor and outdoor tracking to environmental monitoring.
The author is Ben Sturgess, co-founder and chief technology officer, Pathfindr.
Comment on this article below or via Twitter @IoTGN