The rise of Industry 4.0 and the Industrial Internet of Things – Part Two
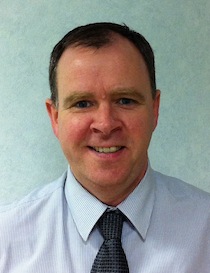
Dave Sutton, Schneider Electric
IIoT is already having a significant impact on industrial performance in two primary areas: asset performance management and operator efficiency, writes Dave Sutton, a product marketing manager at Schneider Electric, in the second part of his blog on Industry 4.0 and the Industrial Internet of Things.
We can see this in the likes of increased deployment of open ethernet based technologies, wireless technologies, cloud connectivity, low cost sensors, the use of advanced data analytics, and new generation control systems capable of handling heightened demands for connectivity and big data management. These technologies, previously limited by the cost of connection or implementation, are enabling the gathering of asset information that supports maintenance programs and decision systems for manufacturing operations. That means that unnecessary routine maintenance can be avoided, as can the neglect of equipment that subsequently fails.
In many industries today, there are fewer and fewer skilled operators inside the plant as the older, expert workforce moves into retirement. IIoT presents a great opportunity to bridge this gap and augment today’s workforce by putting real-time status and diagnostic information at their fingertips. It can also make it simple to enable mobile phones to scan dynamic QR code error messages for rapid troubleshooting. Other examples include the use of smart tablets and industrial automation apps, all of which are providing simpler, easier to use, richer information to the operator, and making the plant user-centric, not machine-centric.
We are in the era when IT meets OT
Most of the fervor associated with IIoT has been at the technology level, which is already gaining acceptance and delivering business improvements today. Particularly in areas like connectivity, asset management and operator efficiencies. In combination, however, these technologies present greater opportunities for smarter manufacturing and with it the potential to remove the constraints imposed by legacy technologies on automation systems in particular.
As the deployment of IIoT technologies continues, we will see further deployment of Open Ethernet technologies across both the manufacturing and device level. The Operational Technology of the factory floor will become increasingly tightly integrated with the Information Technology of upstream business systems – IT meets OT. Architectures will become flattened, and with these new levels of agility, automation systems will be perfectly matched to industrial process topologies. This will simplify the application and operation of both. IIoT will also allow automation applications to be aligned fully to the process, independently of the automation hardware. Tightly integrated systems will distribute the application transparently to the hardware, configuring all communication mechanisms automatically, and allowing the connected devices to publish important information in a standardised format. Intelligent brokers will make this information available in a transparent manner to the systems and applications that require it.
Smart organisations are already on the IIoT road, phasing in new technologies alongside their installed base systems in order to start reaping the benefits.