Flowfinity boosts manufacturing efficiency with IoT and real-time OI
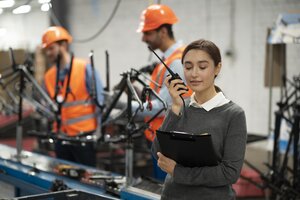
Image by Freepik
Flowfinity is helping manufacturers deploy custom industrial IoT solutions with real-time Operational Intelligence (OI) to prolong equipment life and reduce material waste.
Operations Managers face significant challenges when it comes to maximising manufacturing ROI. Teams can’t easily make up production lost to unscheduled downtime due to breakdowns. Meanwhile, inflation has raised the cost of raw materials, so any anomalies in production are more expensive than ever.
Flowfinity is helping organisations of all sizes gain a competitive advantage by offering scalable OI Dashboards connected to IoT data and human-driven workflows. Now, managers can gain real-time insights into production without programming complex hardware and software to respond quickly to anomalies.
Flowfinity M1 Controllers are natively compatible with Flowfinity workflow automation and data visualisation software. They can be retrofitted to existing machinery to monitor energy consumption, temperatures, pressures, line speed and environmental factors that can affect production quality. When there is a discrepancy, Flowfinity automation will take corrective action to prevent waste or send alerts to trigger preventative maintenance and prolong equipment life.
“Over two thirds of manufacturers believe IoT and real-time Operational Intelligence would increase their competitiveness. However, many of our clients were struggling with the complexity of programming hardware to connect with their core systems and workflows.” said Larry Wilson, a vice president. “That’s why we’re empowering manufacturers of all sizes to connect their people, processes and facilities with scalable IoT solutions that managers can deploy from endpoint to server without coding or straining IT resources.”
To discover how you can gain real-time operational intelligence to maximise uptime and production quality, read: Real-Time Operational Intelligence Is Achievable with Flowfinity IoT Solutions.
Comment on this article below or via X: @IoTGN