Artificially intelligent industry: How to introduce AI successfully into an industrial business
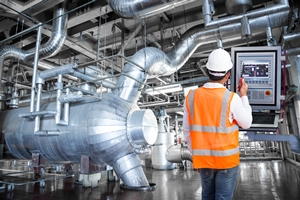
It might be a common term that is integral to most modern technology, but the phrase artificial intelligence (AI) itself was only coined little over six decades ago. While the worry of sentient systems usurping responsibilities from humanity is age-old and persistent, AI itself is playing an increasingly valuable role in managing industrial business operations. Here, Tobias Antius, CEO of industrial automation expert Novotek, explains how AI is benefiting industry.
According to numbers reported in March 2018 by Voicebot.ai, one in five adults in the US have access to a smart speaker and artificial intelligence (AI) powered virtual assistant. AI assistants have similar popularity elsewhere in the world; China is predicted to have 85.5 million smart speaker users by the end of 2019, and there is soon to be 22 million smart homes across Europe.
These numbers show that society is becoming increasingly accustomed to the use of AI and automation to make everyday processes more efficient, effortless and convenient. This isn’t just a domestic shift. We’re seeing industrial businesses investing more in automation systems and AI to provide the same efficiency in complex industrial environments.
Of course, AI in industry means more than a plant manager simply installing a smart speaker in their office — though this is something that could be done for hands-free status updates if connected to a SCADA system, as we explained in our recent industrial automation whitepaper. More often though, incorporating AI into industrial systems involves the integration of Machine Learning (ML) algorithms into Industrial Internet of Things (IIoT) platforms to manage, monitor and control systems.
AI for maintenance engineers
In recent years, the IIoT has become an unavoidable topic of conversation for most engineers and plant managers. Data has become increasingly valuable, in line with the development of technology able to collect new operational and performance metrics and the growing adoption of cloud-based infrastructure, giving managers and supervisors the tools to remotely monitor systems in near real-time.
According to statistics provided by Riello UPS, the typical smart factory produces approximately five petabytes, or five million gigabytes, of data every week. Not only is this volume of data more than a human can efficiently analyse manually, but it’s also an ample amount of information for a ML algorithm to learn from.
This is one of the core applications of AI in the industrial sector. With a complex network of systems and equipment in a typical plant, AI can provide extensive, effective insight into operations in a fraction of the time that it would take a human. For plant managers, this means many of the more analytical management tasks can be automated to improve efficiency.
Maintenance is a prime example of this. The constant stream of operational data from smart systems can be analysed in real time by AI, which can highlight any consistently outlier data readings to maintenance staff through an alarm system. This supports a culture of proactive maintenance rather than reactive, which in turn will help minimise downtime — both scheduled and unplanned.
Crucially, ML means that the system can learn to identify the normal operating range for data from individual pieces of equipment, reducing the number of incorrectly identified issues. It can also quickly spot correlations between different data sets, which an engineer may not be able to identify in a timely manner.
A single machine can contain dozens of sensors or other health signals. To get a clear picture of all the things that affect reliability, that data should be evaluated alongside things like maintenance records and a history of what the machine was running. Even ambient conditions and crew data can help spot the issues that can crop up.
The only effective way to navigate the abundance of variables is with an IoT platform with machine learning, such as GE Digital’s Predix platform. Predix’s machine learning algorithms can analyse equipment with advanced analytics, providing businesses with valuable insight. Rather than just identifying what a problem is, the AI can present a reason why that problem is occurring.
For example, a food and beverage manufacturer might find that a fault in the production process is leading to one fifth of every batch of dairy product spoiling. This process has far too many data points for a maintenance engineer to reasonably analyse, while Predix is able to quickly assess the performance data from that production line.
In this specific scenario, Predix doesn’t immediately highlight any equipment as behaving abnormally or significantly out of ordinary parameters. What it does identify, however, is that the batches that are wasted correlate with a specific member of staff supervising the production line. In this case, the problem might be the result of staff error. An alert could then be sent to the line supervisor to highlight the correlation.
This is certainly a valuable feature of industrial automation software, effectively making performance data analysis an automated process. Yet there is much more than can be achieved by using AI in digitalising and automating maintenance.
Intelligent systems
The reason why ML is specifically valuable when integrated into an IIoT platform is because it allows detailed simulations of possible operational scenarios based on collected data. GE Digital’s Predix, as an example, can use this data to create a digital twin of a plant, in which the plant manager can use the AI to visualise how actions — or inaction — might affect systems.
With this, predictive maintenance becomes a reality. The AI can run simulations and predict when a piece of machinery will require maintenance, which means maintenance engineers can avoid non-value-added time by only attending to equipment at the optimal time.
In fact, there are certain industrial applications where the algorithms could directly reconfigure a machine with the right settings, in instances where it identifies an issue. And as machine algorithms learn, this will become an increasingly viable way of improving efficiency.
We have learned a lot in the last six decades since the term AI was coined, and both we and modern ML systems will learn much more in the decades to come. One thing that remains apparent is that AI systems are helping humans achieve more, efficiently and effectively, and providing the potential for greater productivity.
The author is Tobias Antius, CEO of Novotek
Comment on this article below or via Twitter @IoTGN