Ericsson Estonia and ABB walk the walk on 5G smart manufacturing
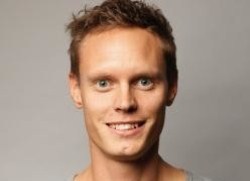
Erik Josefsson of Ericsson
With 5G a growing reality and Industry 4.0 underway, Ericsson is taking a big step toward smarter wireless manufacturing and automation at its own 5G factory in Tallinn, Estonia.
In partnership with ABB, Ericsson will deploy an intelligent automation system at its manufacturing facility in Tallinn throughout 2019, beginning with the Ericsson Radio System portfolio.
Ericsson will subsequently combine this system with its own connectivity layer – adding Machine Learning and Artificial Intelligence to its production, enabling real-time data analytics and an end-to-end predictive automated manufacturing chain.
As part of the recently signed local agreement, ABB will provide a fully automated flexible robot cell solution for final assembly of 5G radios.
Ericsson and ABB enjoy a long-term collaboration, including several ongoing joint research and development projects across 5G and industrial automation. In 2017 Ericsson and ABB introduced a 5G lab in Västerås, Sweden. With this deal the two companies can now move more robotics and edge communication collaboration to Ericsson’s real shop floor environment.
Lars Ottoson, head of Ericsson Supply, Tallinn, says: “This investment will help consolidate Ericsson’s instrumental role in the evolution to smart manufacturing, as well as catering to future 5G-automated, high-volume production demands at our own manufacturing facilities.”
Enabled by 5G and ultra-low latency connectivity, smart manufacturing is widely expected to be deployed exponentially over the coming years. New standards within cellular connectivity make it possible for businesses to connect almost every factory asset: automating the supply chain, ensuring operational efficiency and quality, and enabling flexible production through cloud robotics.
Erik Josefsson, head of Advanced Industries, Ericsson, says: ” Ericsson and ABB can now drive innovative collaboration across the industrial ecosystem together in Tallinn to enable the future of wireless and automated production.“
As highlighted in Ericsson’s recent special edition World Economic Forum Mobility Report, digital transformation to smart manufacturing will be enabled through a large network of sensors for predictive maintenance of machines/robots on the factory floor; cloud robotics; identification and tracking of goods in the end-to-end value chain; and remote diagnostics through high-resolution, 3D video or haptic sensors.
Ericsson’s smart factory is expected to be fully operational by the end of 2019.
Comment on this article below or via Twitter @IoTGN