IoT and additive manufacturing: Towards an intelligent and connected world of electronics
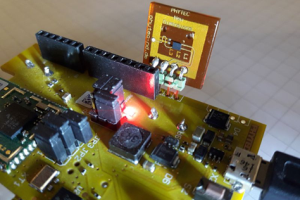
Phytec’s PCB sensor for ambient
temperature and relative humidity printed
on Nano Dimension’s DragonFly Pro System.
“Alexa, dim the dining room lights.”
Five years ago, that would have been a command to a human. Today, Alexa is but one virtual personal assistant among vast networks of interconnected “smart” devices totaling 8.4 billion units that is taking the world by storm.
The concepts behind this “Internet of Things” or IoT is simple: Connect devices to each other and the Internet by building sensors and transmitters into them, so they can “communicate” and collectively serve a function better than if each were operating individually. The IoT concept stretches back to the 1980s, but the enabling technologies — RFIDs, reliable sensor networks and an updated internet protocol (IPv6) — that can accommodate billions of connected devices wasn’t ready till the 21st century.
The ingredients for functional IoT systems have been in place for years, but thanks to high R&D costs, time, and risk, there are no perfect IoT solutions today. There is, however, reason for optimism.
The recent advent of additive manufacturing for printed electronics, for example, has made engineering and design labs game-changing R&D enablers. The greater design freedom, compressed project timelines and fully in-house workflows afforded by 3D printing are setting the stage for the long-awaited IoT revolution.
Strength in numbers and networks
One of the IoT’s greatest promises lies beyond the reliable logic structure it offers. In bringing many autonomous systems together, IoT systems can communicate and interpret data at a level unfathomable by human intelligence. Insights gained from a larger ‘big data’ pool make possible any number of new possibilities in efficiency, scale and performance. With the ability to automate all the processes above, IoT systems are heralding a major shake-up in how we use and benefit from technology in real-time.
Accelerating IoT prototyping
Every IoT system has at least two key components: sensors and connectivity devices like radio-frequency identification (RFID) tags and antennas. These electronic components all typically feature complex, multi-layered circuitry. Manufacturing these printed circuit board (PCB) components layer-by-layer using traditional subtractive manufacturing methods such as copper etching, followed by post-processing steps to combine them into one unit, usually takes days or even weeks.
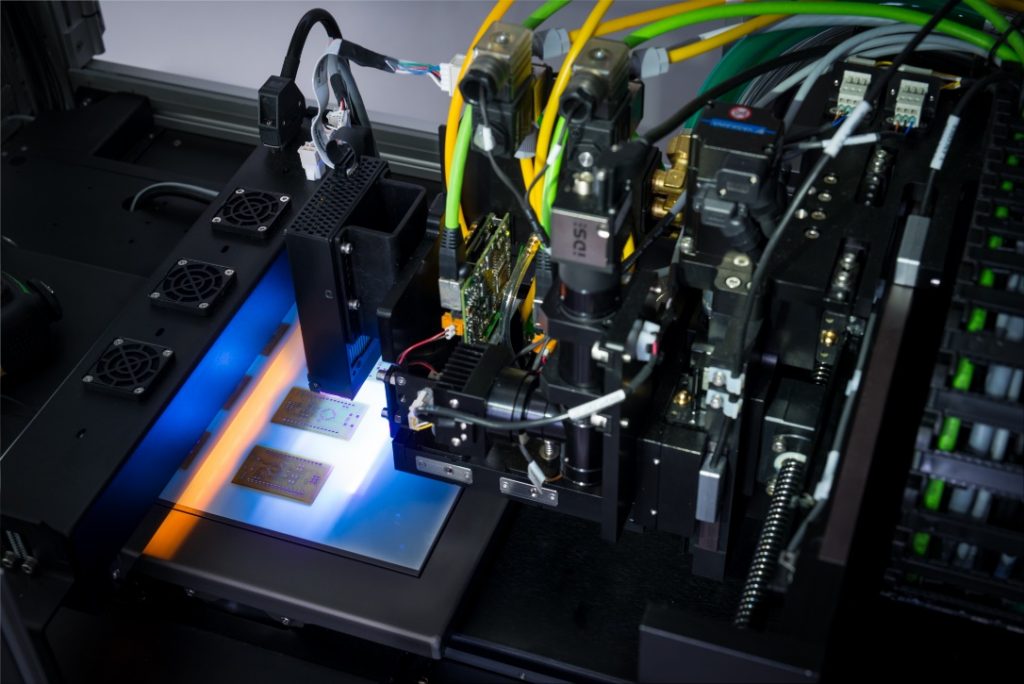
Nano Dimension’s DragonFly Pro System building up PCB layers through additive manufacturing in an in-house process that saves both time and cost.
Research labs typically do not have bulky PCB manufacturing equipment in-house, so designs must be outsourced or offshored for manufacturing and testing sample products, adding extra time, cost and increasing the risk of intellectual property (IP) theft.
That’s where additive manufacturing for advanced electronics can help. This advanced branch of 3D printing offers the ability to create objects through material deposition (instead of abstraction) at very precise levels to PCBs, molded interconnect devices (MIDs) and other components.
A key advantage to 3D printed electronics is lower material costs because close to exact amounts of ink are extruded to 3D print each component. In contrast, traditional manufacturing methods such as copper etching waste 50% to 70% of the original amount of copper used.
Beyond material costs, modern additive manufacturing systems for electronics offer other advantages for IoT system designers and engineers. Nano Dimension’s DragonFly Pro system, for example, enables design freedom, agile workflows and production speed, due to its simultaneous deposition of both dielectric polymer and conductive traces to produce functional circuit prototypes.
As a compact factory-in-a-box, the DragonFly Pro system brings prototyping and IoT component manufacturing from large wet-process factories to much smaller lab and office spaces. This enables true in-house development, free of IP risks and transport costs associated with third-party sub-contractors.
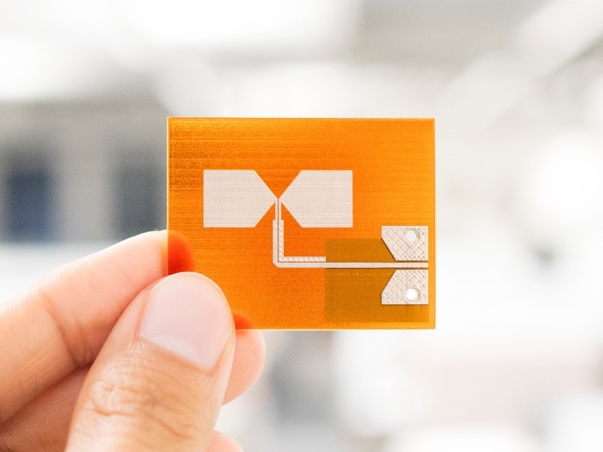
Nano Dimension’s precision 3D printed 5G antenna
New IoT designs possible with additive manufacturing
3D printed electronics improve upon current manufacturing methods in terms of time, cost and risk, and the additive process also allows for new component designs that are currently difficult, if not impossible, to achieve with subtractive methods.
For sensor design, additive manufacturing eliminates many traditional limitations, especially those related to planar electrical designs. The result is highly customised surface topographies can be created to facilitate angled placement of sensor components and incorporate multiple functions in a single device. In antenna and RFID tag production, the ability to create miniaturised flexible electronic structures means that they can be placed on more products and locations.
Today’s additive manufacturing technology from companies like Nano Dimension eliminate the limits and machine constraints of traditional electronics development. Now the only limits are human creativity.
The important question then becomes: How will you envision the future of additive manufacturing and IoT?
Comment on this article below or via Twitter @IoTGN