Five product trends to keep an eye for improvement of new or future iterations of products
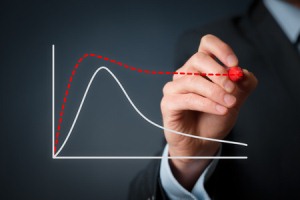
You can always count on change as a constant in the Internet of Things (IoT). Here, David Grammer, PTC UK’s senior vice-president, describes five product trends we should keep an eye out for. The way that manufacturers manage information throughout the product lifecycle has changed significantly in the past few years.
The Internet of Things (IoT) has helped accelerate innovation in the design process, making it possible for manufacturers to receive information from products in the field that can be leveraged to improve new or future iterations of products. In order to succeed, organisations are going to need to embrace new technologies and capabilities available through enterprise system vendors.
Here are 5 trends in product design that engineers are going to be seeing and leveraging in the coming year:
- Augmented Reality (AR) in design review
As teams become more globally distributed, it can sometimes be difficult to get everyone involved to review a product design in a timely manner, collect all the information needed for the review, and capture feedback for future action.
Using augmented reality (AR), team members are able to visualise, interact with, and provide feedback on product designs from anywhere in the world. AR makes it possible for stakeholders to interact with a 3D model of the product, such as walking around it and viewing different states of the model – including going inside the model itself. AR also enables users to get a third-party perspective from other teammates. This particularly comes in handy when deciphering notes from a colleague as it brings you to the point of view of the model they had when they made the comment.
- IoT products transforming design practices
The market is clamoring for smart, connected products: whether it’s an Amazon Echo, a Nest Thermostat, or a Fitbit. In order to sufficiently meet the expectations of customers, manufacturers need to transform their product development process to understand and leverage data from products in the field. Noting product information on a CAD drawing is no longer going to cut it as products become more complex. Manufacturers will need to become more organised with their product development process.
Having a comprehensive PLM system provides a strong foundation to taking full advantage of IoT capabilities. By consolidating all product information into a single-view digital product definition, organisations can ensure that stakeholders are all accessing the most accurate, up-to-date product information. With a PLM system, all information is streamlined into a single easy-to-read Bill of Materials (BOM) list format.
- Digitalisation
Product data is an organisation’s most valuable asset. With products gathering data from the field, this data is becoming more valuable every day. However, many organisations continue to keep it locked away with engineering and manufacturing. Product data can be leveraged throughout the enterprise: whether it is how the marketing team promotes the product or how the sales team sells it.
By digitising the product development process, stakeholders throughout the organisation will be able to easily access product information. For example, if a manufacturer just merged with or acquired another company, digitising the product development process and making product information accessible to all stakeholders ensures that there’s no infrastructure disparity between organisations.
Digitalisation also ensures compliance of industry standards throughout the product lifecycle. This is especially key for highly regulated industries such as the medical device or automotive field. Being able to pinpoint the root cause of issues and track changes throughout the lifecycle ensures that manufacturers are able to successfully meet industry standards.
- PLM and digital twin
Having a window into how each product or asset in the field is operating is key to improving profitability, decision making, and ensuring security, legal, and regulatory compliance. With a digital twin, the digital definition is combined with the specific physical experience of the asset, for example environmental conditions and performance data from an operating asset. This purpose built digital representation allows manufacturers to analyse assets for future sales, recalls, or update opportunities. Real-world usage can be leveraged to improve future products or future iterations of the products.
- PLM in the cloud for rapid transformation

David Grammer
In order to stay competitive, it is imperative that manufacturers rapidly transform their product development process. Enabling this is the ability to host their PLM and other enterprise systems in the cloud. Cloud based PLM removes the burden of setting up and maintaining the system on-premise while also reducing the cost of owning the system. Forget managing your enterprise systems on the cloud. More and more manufacturers are relinquishing the burden of setting up and maintaining their PLM system on-premise.
PLM in the Cloud makes it possible for manufacturers to rapidly deploy their PLM solution and begin to see results sooner. Deploying in the cloud also reduces the burden of hosting the server.
Alternatively, many companies are looking to host their PLM solution as SaaS. SaaS offers many the same benefits as the cloud with the added bonus of the PLM vendor handling all upgrades, updates, and software migrations for the customer.
Whether your organisation is evaluating whether to deploy a PLM system in the cloud, it’s ready for a part-centric approach, is looking to digitise, or is ready to incorporate augmented reality or build a digital twin, 2018 will be an exciting year for those on the product design team.
The author of this blog is David Grammer, senior vice-president of PTC UK
Comment on this article below or via Twitter @IoTGN