The Industrial Internet of Things: A boon for small and medium-sized manufacturers- Part 2
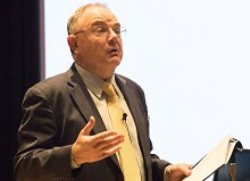
Alain Louchez of Georgia Tech
Nothing new, but certainly still worthy of emphasis: smaller manufacturers represent an essential and dynamic component of the U.S. manufacturing industry. The Part 1 of the article yesterday consisted of smart manufacturing, digital manufacturing, digital transformation etc., the continuation of the article lies below.
Digital transformation still in early stages among SMMs
Very tellingly, a March 2017 White Paper from the World Economic Forum on Technology and Innovation for the Future of Production: Accelerating Value Creation quotes a recent study of 4,500 German SMEs, which “found that fewer than 20% had heard of Industry 4.0, much less taken steps to implement it”, say Mary Bunzel and Alain Louchez.
It is quite a finding when we recall that the very concept of Industry 4.0 was born in Germany! The World Economic Forum White Paper ominously adds “this highlights the challenge many countries will face in assisting their small and medium-sized producers to reap the value of technologies.”
A 2015 White House press release relays the same kind of observation: “because of the unique barriers they face, small manufacturers often lag their larger peers in adopting critical new technologies. For example, a recent survey found that fewer than 60% of small manufacturers were experimenting in any way with 3-D printing, a potentially transformative technology that is especially beneficial for small companies due to its flexibility. In contrast, over 75% of large firms were using the technology.”
Yet, SMEs have a lot to gain from exploiting IIoT technologies to generate cost-cutting efficiencies and new revenue streams.
SMMs tend to be highly specialised, offering skills larger manufacturers can’t afford to maintain. Deep domain expertise is key to the development of analytic algorithms necessary for compute at the edge, digital twin specifications and artificial intelligence – just a few elements of Industrial Internet of Things technologies.
This domain expertise in combination with natural agility that comes from more nimble corporate structures creates fertile incubation for truly disruptive market opportunities through leverage of IoT-based tools.
For instance, a journeyman boilermaker, having spent 30 years maintaining the steam supply to production facilities at a food processing plant made the decision to retire. But like so many deeply experienced professionals, he sought to share his extensive knowledge on the science of hydraulics and to stay involved in industry best practices. Teaming with a supply partner he had worked with in the past, he worked with data scientists at the partner firm to incorporate operational models for steam feeds, hydraulics and boiler conditions into mathematical algorithms the firm was building into their IoT Platform for Industry.
Using the knowledge of variable conditions affecting steam performance gained over 30 years, he was able to help the partner develop condition models of performance that became part of an analytic platform available through subscription to any company needing the expertise.
In June 2017, MForesight: The Alliance for Manufacturing Foresight (a national consortium established in 2015 to provide coordinated private‐sector input on national advanced manufacturing technology research and development priorities) published a report on Ensuring American Manufacturing Leadership Through Next-Generation Supply Chains. They argue that for US manufacturers “regaining a competitive edge requires a different approach to managing suppliers, one in which the total supply chain is managed to maximise value.”

Mary Bunzel
As a result, “private companies, large and small, will need to reassess their approaches to supply chain management using the tools and best practices that have proven to be successful and that lay the groundwork for full implementation of next generation supply chains.”
The MForesight report stresses that not only U.S. suppliers are especially important to the overall health of domestic production since 80% of gross output is domestic content, but also that the role of small and medium-sized enterprises (SMEs) in supply chains is “critical to manufacturing success”.
What path forward for the SMMs?
As far as the SMMs that have not yet triggered the digital switch, it is paramount that they understand that they can benefit on two levels from IIoT:
- Directly: advanced manufacturing technologies should facilitate the development of efficient and nimble operations that bring about substantial productivity gains.
- Indirectly, as part of a broad supply chain: “after a small supplier lands a big purchase order or a contract from a bigger company, the small company’s revenues go up 250% and they create about 150% more jobs in just two or three years,” (SBA website). In this case, the SMMs’ systems have to mesh seamlessly with those of the large firm. In all likelihood, they will have to demonstrate the same (presumably high) level of automation and integration to ease their insertion within a bigger whole.
In the latter case, they will have to show, before anything else, than they can be “trusted”, i.e., they exhibit tight trustworthiness management capabilities. Such capabilities suggested by the National Institute of Standards and Technology (NIST) in its Framework for Cyber-Physical Systems (Release 1.0, issued in May 2016 and updated in June 2017), are cybersecurity, privacy, safety, reliability, and resilience.
Undoubtedly, many challenges lie along the way regarding the utilisation of IIoT technologies by SMMs, but they can be overcome. Recommendations on implementing capability upgrades are at the core of the recently introduced Smart Manufacturing Leadership Act and included in the above-mentioned Supply Chain Innovation and MForesight reports; some of them centered on established programs the likes of the Manufacturing Extension Partnership (MEP) and Manufacturing USA.
In addition, the use of cost-effective tools such as modeling, emulation, simulation or novel approaches such as gamification can assist in smoothing out the transition to an IIoT-framed production environment.
The authors of this blog are Mary Bunzel, director, Manufacturing and Industrial, Industrial Sales & Marketing Group, Intel Corporation and Alain Louchez, managing director of the Georgia Tech Centre for the Development and Application of Internet of Things Technologies (CDAIT).
The views expressed in this article are solely the authors’ own and do not necessarily represent those of Intel Corporation, the Georgia Institute of Technology (“Georgia Tech”), the Georgia Tech CDAIT members, the University System of (U.S. State of) Georgia or the (U.S.) State of Georgia.
Comment on this article below or via Twitter @IoTGN