Why force sensing has the power to revolutionise human-machine interfaces
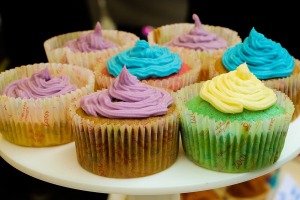
The first time I set foot on a Boeing 777, I was blown away. Not by the advanced aero engineering all around me, but by the fact that every seat had its own TV screen.
And these weren’t just any TV screens – these were full-on touch displays that enabled each of the 300+ passengers to watch whatever we wanted at 37,000 feet above the Earth. Things have come a long way since then both technologically and socially, with touch interfaces having revolutionised the way we interact with everyday items and content.
Touch screens quickly became a popular way of interacting with machines, promising to improve this so-called human-machine interface (HMI). Whether we’re talking about industrial machines or consumer electronics, the quality of any HMI owes itself to how intuitive and enjoyable the experience is.
Accidentally ‘pocket-dialling’ your mother-in-law is something you can laugh about. Accidentally turning off the oven by leaning against the control panel — causing the cake you were baking for your child’s fourth birthday to be ruined — is definitely not something you can laugh off, says Jon Stark, CEO, Peratech.
As you deal with the inevitable tears from your little one, the people who dedicate themselves to engineering the best possible HMIs get down to work. Our job is to create the right user experience on every device, every time you use our tech.
A brief (recent) history of HMIs
Going back a few years, physical buttons started being replaced by resistive touchscreens. Initial user excitement with resistive touch technology quickly became frustration, which is one of the reasons resistive screens have been superseded by capacitive ones.
The launch of the iPhone and iPad really brought capacitive touchscreens to the masses, showcasing both the elegance and limitations of this type of touch control. We marvel at its intuitiveness as our toddlers pinch to zoom in and out of pictures in an ebook. But at the same time, we get frustrated as we tap out an email one-handed, get a few letters wrong and autocorrect kicks in to change the meaning of our message entirely — with hilarious or sometimes embarrassing results.
Challenges for capacitive touch
The success of smartphones and tablets shows we clearly love touch HMI, but it isn’t perfect. From a technical standpoint, capacitive touch is challenging to implement: sensors have difficulty pinpointing the exact touch location, even on a flat surface under optimal conditions.
Make that surface curved or even flexible, or add heat, moisture or gloves to the mix and capacitive touch really struggles to deliver the experience consumers and tomorrow’s product designers want.
Force sensing: Is it a game-changer?
There’s been much interest recently around force sensing and its ability to enhance HMIs. Force sensing occurs when a sensor is able to generate an electrical signal in relation to the amount of force you apply. If you can add force sensing with precision, reliability and repeatability into an HMI, you unlock a whole new way to interact with and control devices.
For example, what was previously a binary on/off touch button can now also be an intensity controller, enabling you to control anything from the brightness of a lamp to the speed of a motor, as you progressively increase or decrease pressure.
Incorporating force sensitivity into consumer electronics creates a brand new HMI ‘vocabulary’ that enables you to incorporate new functions and cut complexity. Moreover, it helps you reduce unintentional presses, because it adds an additional key data point to systems.
Millions of people are already experiencing force-sensing tech in Apple’s products, as either ‘Force Touch’ or ‘3D Touch’ in the Apple Watch, MacBook, Magic Trackpad 2 and iPhone. These technologies promise to make interacting with the device and apps easier and quicker.
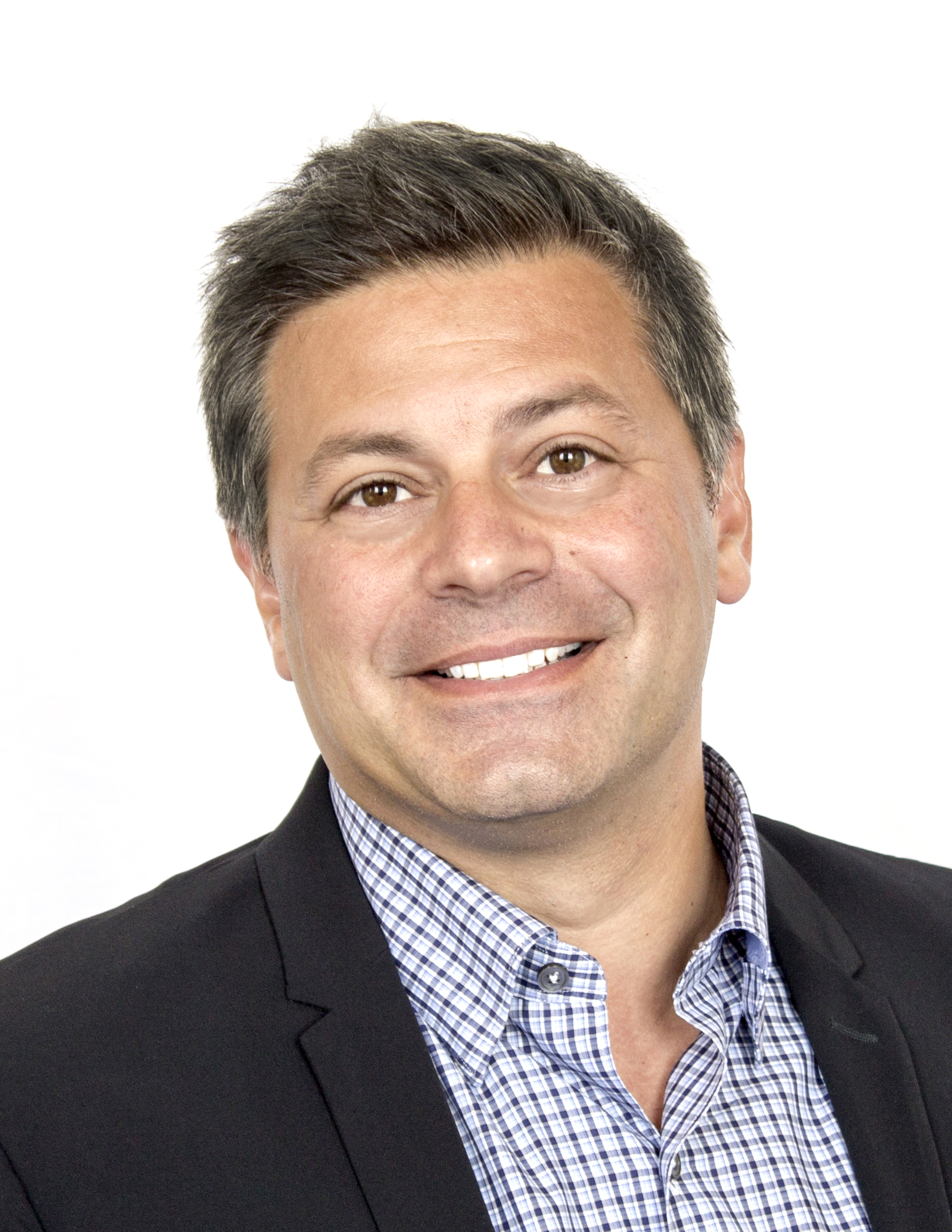
Jon Stark, CEO, Peratech
Making force sensing work
There are several ways we can use electronics to measure force. These include Force Sensing Resistors (FSR), Projected Capacitive, Optical, Piezoresistive, MEMS and Strain Gauges. Whichever technology you use, the sensor must meet a number of requirements before it will be designed into any consumer device.
It must be thin and easy to integrate into your product. It needs a lifespan stretching to millions of presses. Its first-touch sensitivity must be good, but at the same time, it mustn’t register false touches. It must be capable of measuring the range of expected forces.
And as if this wasn’t challenge enough, it must be able to perform according to its specification, even in adverse environmental conditions. As with so many things, each force-sensing technology has different strengths and weaknesses.
Quantum Tunnelling Composite: a unique solution
At Peratech, we exploit a known phenomenon called Quantum Tunnelling to create a variety of force sensing solutions. To make our sensors cost effective in mass production, we’ve incorporated this Quantum Tunnelling effect into budget-friendly, screen-printable flexible polymer composites that we call QTC. Force sensors that use QTC offer a unique solution to many of the problems encountered with other technologies.
With no force applied to QTC, it’s a great insulator, and the sensor itself uses no current. But as you apply pressure to it, its conductivity progressively increases. What’s more, QTC-based sensors can be made into any shape or size that you can screen-print. We believe that this combination of attributes makes QTC based sensors an ideal choice for many applications — including oven control panels.
Sadly, it’s beyond my powers to rescue that birthday cake, but I can help others around the world to create ever-better human-machine interfaces.
The author of this blog is Jon Stark, CEO, Peratech
About the author
As CEO at Peratech, Jon Stark leads a talented team innovating the next generation touch technology solutions with Quantum Tunnelling Composites (QTC) technologies. He is committed to driving groundbreaking developments in QTC materials for an expanded range of uses in consumer, automotive, industrial and medical applications. He bakes yummy cakes with his daughters as often as he can.
Comment on this article below or via Twitter @IoTGN