Autonomous vehicles and industrial robots: network infrastructure
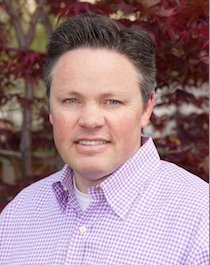
Todd Rigby, Rajant
In his last blog, Rajant Corporation’s Todd Rigby discussed the impact of autonomous applications and robots on industry and the need for ironclad network infrastructure to ensure autonomous vehicles and industrial robots operate flawlessly. Here, he discusses the major role mesh networks play in providing the real-time, continuous communications required to run these machines.
Industrial robots and autonomous applications are ushering in a new age of smart, connected machines, but they require highly reliable, mobile, resilient communications networks that run continuously and ensure data is never delayed or not received. Kinetic Mesh networks have demonstrated their capabilities in multiple sectors, including autonomous use cases, and can be part of a future that improves human lives by putting robots to work.
In a Kinetic Mesh wireless network, each node serves as singular infrastructure, which enables all devices and the network itself to be mobile. It employs multiple radio frequencies and any-node-to-any-node capabilities to continuously and instantly route data via the best available traffic path and frequency, using hundreds of nodes.
If a certain path becomes unavailable for any reason – due to antenna failure or power loss to a piece of equipment, for example – nodes on the network use an alternate route to deliver the data, eliminating any downtime.
The network never fails as a whole; data is sent and received simultaneously, in real time. Multiple hops do not add measurably to transport time. The networks operate with the same level of reliability even in the harshest conditions. There are no single points of failure, and the network can be redeployed in multiple ways simply and easily.
Because there is no central control node, routes are built automatically, and are evaluated for quality and performance with every received and sent packet. This artificial intelligence allows the network to adapt to node location, local interference and congestion dynamically despite conditions that would cripple other networks.
Kinetic Mesh has been successfully used in multiple industry segments for mission-critical autonomous applications.
Oil & Gas
After an oil well is drilled, a down-hole pump brings the oil to the surface to be collected and processed. The well heads have data loggers, which workers use to set the pump speed. Setting a speed that is too fast risks the hole running dry and the pump burning up, so workers naturally operate wells on the conservative side. A burned-up pump may cost thousands of dollars to replace, but the total repair and removal price can skyrocket into the hundreds of thousands of dollars.
Workers only visit the pumps every week or so, so pump speed is determined based on data that is outdated as soon as the worker leaves the field after each visit, creating production loss.
A Texas oil company set up a Kinetic Mesh network to connect the pumps and send all production data to a central office in real time, eliminating any need for a technician to go into the field to pull data from each individual well. Now, technicians in the central office are alerted immediately if there is a drop in production on any well. This allows the technicians to fine tune the pump speeds for optimal oil field production.
The pumps are not fully autonomous, as technicians still manually adjust speed as needed, but the Kinetic Mesh network has enabled remote operations of equipment as well as allowed the company to run the pumps at exactly the right speed based on the oil conditions of a given well, increasing profits and providing a positive return on investment within a matter of months.