FACTORY FLOORS IN THE CLOUD
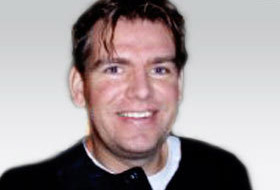
M2MAPPS: Can you start by outlining how you started?
ARNOLD AGEMA: I entered m2m via the back door. I’d been running an IT company in the Netherlands that specialized in industrial automation and in 2008 I was approached by a Dutch OEM that had been operating worldwide since 1985. They had issues with the way they made remote connections to their machines and could not find a good solution. They knew what they wanted and what their customers needed, but they didn’t have the right technical resources and knowhow. My company did, so together we started developing a remote m2m servicing and management solution and it turned out to be a much tougher challenge than I thought. That’s probably the reason why nothing suitable was on the market at that time. It took a couple of years to develop but together we realized a solution that did the job.
M2MAPPS: What was the next stage?
ARNOLD AGEMA: I had to make a business decision. I could see that there was still a gap in the market so there was a significant marketing opportunity. I discussed it with the partner company and we decided to do more development work in order to create an open system. That took some time, but after extensive testing we decided that we had a robust, innovative offer so we formed a new company called Remote Engineer and in 2010 we took the solution to the marketplace. I can’t say that the rest is history, but we have enjoyed considerable success. I put that down to the fact that we came from the direction of the factory floor.
M2MAPPS: The name is interesting. It encapsulates the functionality.
ARNOLD AGEMA: Exactly. The solution allows companies to securely and simply access and manage equipment through a VPN tunnel to each asset at third party locations, even those that are behind firewalls. The installation is plug & play and the ongoing management of the connections is automated. And because this connection is transparent, customers can access the machine with their own diagnostic tools from their own development environment.
M2MAPPS: How do you enable plug & play connectivity?
ARNOLD AGEMA: It’s enabled by our support for different communications protocols and networking ports. In addition we configure the routers in advance. These default settings match the customers’ individual needs and the information is stored. When a customer orders a new router the default configuration will be loaded.. This way the settings that need to be done on the customer site are limited to choosing the right connection to the Internet.
M2MAPPS: There doesn’t appear to be more than a small handful of vendors operating in the space. Why is that?
ARNOLD AGEMA: To be honest I don’t know, although it’s good for Remote Engineer. It could be because you need to combine knowhow and experience in two radically different industries: high-tech M2M connectivity and the factory floor. That said, the business case for minimizing the need for technicians visit sites in order to service machines at regular intervals is solid, particularly when no corrective action was needed. In addition to the time and cost savings, remote servicing and maintenance is a green solution because no travel is involved. This allows us to provide a quality service using just two or three highly qualified technicians. On top of the connection part of our solution we decided to add a case and call service log, which prompts the technician to enter a status report and if required, any follow-up action. Customers can therefore get an overview of the system’s performance and reliability and it also serves as an online reference. Technicians can see what was done in the past when the same or similar issues arose.
M2MAPPS: How do you see factory floor solutions developing in future?
ARNOLD AGEMA: I see a more and more demanding market for information from the factory floor being accessible from anywhere in the world. We aim for a solid and easy to use solution to assist service based companies to achieve this.
Company: Remote Engineer
Remote Engineer provides customers with a solution to communicate with their machines anywhere in the world from anyplace in the world. The company has provided a variety of global customers this solution and they are now able to easily remote-support their machines at any time and place. Remote Engineer, simply connect and control.